As autonomous vehicles (AVs) become a defining technology of modern transportation, the need for precision-engineered components grows exponentially. The development of autonomous vehicles depends on constant testing, continuous improvement, and verification that the components can withstand actual application. To accomplish this agility, low-volume manufacturing provides an effective approach to enabling engineers to make parts economically and quickly in small lot sizes instead of waiting for full production tools.
CNC machining is at the core of the development of autonomous vehicle technology. The process ensures high-speed production, a high degree of precision, and a variety of materials usable. It offers a strong mix of speed, accuracy, and material variety. During the early stages of testing, CNC machining offers engineers parts of the same quality as would be obtained if the operations were carried out in full production. Regarding industrial design prototyping, forming accurate components as soon as possible eliminates delays and minimizes the chances of costly mistakes.
Contents
CNC Machining vs. Other Prototyping Methods
Despite the two, 3D printing and injection molding have significant roles to play in the development of products, neither fully satisfies the needs for prototyping in the autonomous vehicle (AV) part. 3D printing excels on the grounds of timely design revisions and elaboration of geometry. The type of materials used seldom provides the necessary structural and thermal resistance needed in important AV parts. Furthermore, the accuracy of parts resulting from 3D printing frequently necessitates further processing, which delays the development cycle.
On the other hand, CNC machining sculpture parts from strong metals or plastics, specifically titanium, aluminum, or Delrin. These materials have a strong nature and stability, making them appropriate for fabricating functional components in industrial design prototyping. CNC services are the most appropriate for parts that involve precise measurements, critical in the assembly of sensor mounts or functional mechanical systems. Achieving this precision level is of particular importance in rapid manufacturing, which places prototypes under real-world scenarios that sync with the look and functionality of the final product.
Rapid Iteration and Testing Through CNC Services
Continuous iteration is the basis on which autonomous vehicle progress is built. Throughout the development of projects from conception to testing, the adaptive analysis for the design cannot be overemphasized. CNC machining also enables rapid changes at little expense and without significant downtime. With the CAD files amended, the engineers are able to produce new parts within days, rather than weeks.
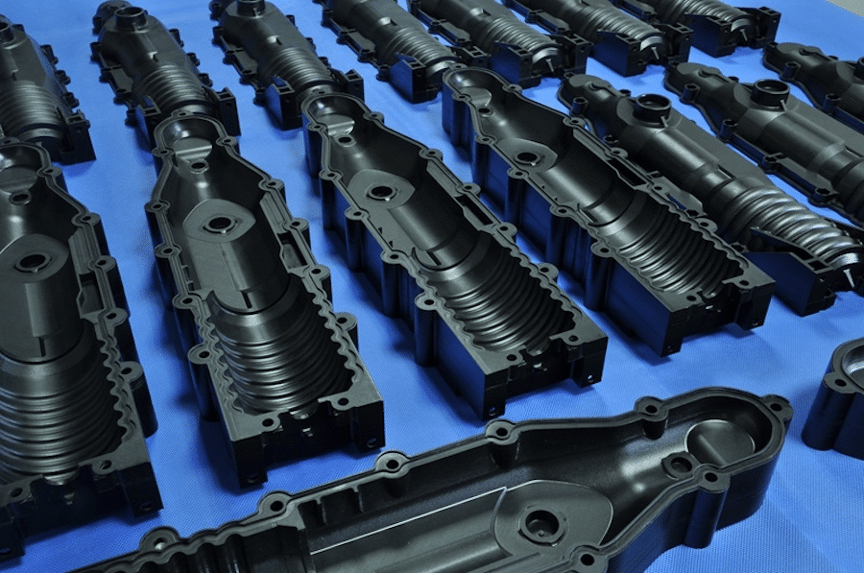
This capability is critical in the scenario of rapid manufacturing, which underscores the necessity to adopt agile manufacturing practices. Using CNC machining, manufacturers can easily create batches of 10 to 1,000 pieces, having precisely consistent accuracy and capable of field testing with actual production material. The CNC machining process aids the construction of the bracketry to be used with sensor arrays or the orderly placement of the GPUs with the assurance of consistent quality, with the ease of modifications.
Several AV initiatives require CNC-machined parts to yield limited-run prototypes or experience pre-production evaluations, which are fundamental before large-scale production. If manufacturers prepackage the precise materials and dimensions for the final products, this enables a simple and rapid transition to mass production.
The autonomous vehicle components must conform to visual and ergonomic standards, other than their mechanical capabilities. Engineers and designers work in industrial design prototyping in order to reach a balance of visual appeal to functional efficiency. CNC machining is better here because it has the capacity to ensure accurate finishes and tight tolerances, and allows the teams to judge functionality and aesthetics alike.
Such reflections will be of particular importance for parts such as control interfaces, dashboard sensors, or touchscreen mounts that play a critical role in the user experience. Using CNC technology, it is possible to create parts that are clones of the final product in the smallest detail, such as the exact contours, and appropriate button openings, and feel realism.
In addition to this, CNC machining also accommodates multi-component sets, thus enabling the design team to construct whole systems and test how assembly components interact with each other. In this way, it allows for mechanical, electrical, and visual alignment of parts, all of which is crucial for the successful implementation of the AV system.
Scaling Production Without Sacrificing Quality
A particular strength of CNC services is that they are easily scalable. The AGV companies may begin by producing only a small number of prototypes, but once the concepts succeed, the transition to bigger test fleets or demonstration units is unavoidable. CNC machining gives the ability to produce volumes of hundreds or thousands while guaranteeing that all parts are made with the same demanding requirements.
This adaptability is critical to rapid manufacturing, where speed and consistency are success factors. Unlike injection molding, where costly mold fabrication is a heavy reliance, CNC machining is able to move along and shoot from production very quickly without a lot of costs upfront. CNC machining is distinguished by its capability to enable the creation of prototype test vehicles critical for certification, on-road demonstration, and evaluation under various weather or terrain scenarios.
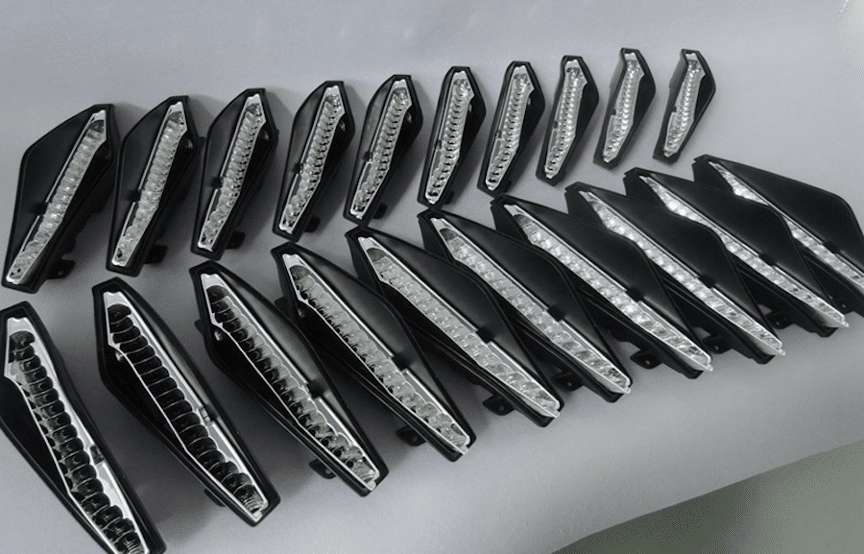
The scalability of CNC machining gives AV developers an opportunity to perfect designs and test them from the prototype stage all the way to commercialization. Engineers can alter designs, react to feedback, and overcome supply chain obstacles before their scheduled product launch, and investor promises.
Material Flexibility and Real-World Reliability
Autonomous vehicles are designed to function successfully in remarkably diverse landscapes, ranging from crowded city centers to empty highways that require components resistant to vibration, water, and extreme climates. CNC machining’s capability to handle a wide range of materials guarantees that it will meet these rigorous specifications. CNC machining supplies materials like stainless steel or aluminum that are outstanding in corrosion resistance and lightweight characteristics, unmatched by most rapid prototyping techniques.
This flexibility is essential in an industrial design prototyping context as it allows for the testing of the aesthetic and functional character of parts. For instance, there is a piece that protects a LIDAR sensor; it must be able to manage thermal buildup, as well as fit perfectly with other neighboring sensors. By using CNC machining, designers can apply production-grade materials to the early prototypes so that the parts behave as expected on field testing. By bringing in high-quality production material early on, AV manufacturers can reduce the risk of facing unanticipated problems and costly redesigns, which is crucial in a ruthless competitive environment with tight regulations.
Conclusion
CNC machining combines speed, material performance, surface quality, and repeatability to meet the complex needs of autonomous vehicle development. Whether for rapid manufacturing or industrial design prototyping, it offers a reliable solution for creating high-quality parts, enabling faster innovation and safer technology. As autonomous vehicles evolve, CNC machining continues to play a crucial role in advancing production, one precision part at a time.